|
风电绝缘轴承表面防护膜的制备及其绝缘性能分析李全伟1,杨斌2,王海3,李永皓3,杜广煜1 (1.东北大学 机械工程与自动化学院,沈阳 110819;2.沈阳飞机工业(集团)有限公司,沈阳 110000;3.沈阳乐贝真空技术有限公司,沈阳 110136)摘要:为提高风电绝缘轴承的力学性能和绝缘性能,延长其在复杂工况下的服役寿命,提出采用磁控溅射法在绝缘轴承陶瓷涂层表面沉积镍膜。通过设计正交试验分析了靶电流、负偏压、溅射时间对镍膜表面形貌的影响以及镀膜对绝缘涂层表面粗糙度的影响,结果表明:随靶电流和负偏压增大,镍膜表面质量提高;溅射时间对镍膜表面质量影响较小,但会影响镍膜厚度;镀膜后表面粗糙度值降低;在靶电流为4 A,负偏压为300 V,溅射时间为90 min时镍膜表面光滑平整,连续性以及膜层致密性最优,为最佳工艺参数。在某风电轴承外表面制备镍膜后,交流击穿电压由6 100 V提高至6 300 V,直流电阻由23 GΩ提高至95 GΩ,绝缘性能提高,说明该工艺的正确性。关键词:滚动轴承;风力发电机;绝缘轴承;磁控溅射;镀膜;表面粗糙度;绝缘性能近年来,风力发电作为一种绿色能源技术,受到了世界各国的广泛关注,逐渐成为重要的新能源发电方式。随装机量增加,风电机组的故障和可靠性也越来越受重视,轴承作为风电机组的关键零部件,其可靠性将直接影响机组的服役寿命。电蚀是风电轴承的主要失效方式[1-4],为解决电蚀问题,常采用绝缘轴承阻断轴电流[5-9],但存在以下问题:1)当绝缘涂层封孔不当,封孔剂未有效填充涂层孔隙时,外界的水分子和腐蚀杂质会通过孔隙进入涂层内部,涂层绝缘电阻下降[10-11],最终导致绝缘性能失效;2)绝缘轴承在运输和安装过程中受外界机械载荷的作用易使绝缘涂层产生裂纹损伤,涂层绝缘性能下降[12-13],且在极化作用下涂层中的电荷会聚集在缺陷处,导致缺陷处电压升高,造成局部击穿[14];3)在运行过程中受转动轴的周期性振动和冲击作用,绝缘轴承会与轴承座产生微动磨损,导致其绝缘性能以及机械稳定性降低[15]。综上分析,有必要在绝缘涂层表面制备一层防护层来提高绝缘轴承的综合服役性能。金属镍膜具有力学性能好、抗腐蚀、耐磨以及抗冲击等优点,可以满足绝缘轴承外层防护的需求[16]。溅射技术的基本原理是利用异常辉光放电产生的等离子体轰击靶材表面物质来制备薄膜,磁控溅射较传统溅射在效率上有显著提升,具有沉积速率快,使用成本低等优势,适合沉积导电性较好的金属或合金靶材,是制备综合性能优良的金属薄膜的主要方法[17-18]。本文考虑利用磁控溅射技术在绝缘轴承陶瓷涂层表面制备镍膜作为保护层,目前关于该方法以及具体工艺参数对镍膜性能影响的研究尚未见报道。本文通过设计正交试验分析靶电流、负偏压以及溅射时间对镍膜性能的影响,以期得到最佳的制备镍膜工艺。1 工艺试验为便于试验,用30 mm×30 mm×5 mm的GCr15轴承钢基片代替轴承套圈,制备绝缘涂层的流程为:喷砂、超声波清洗等预处理→喷涂过渡层→喷涂氧化铝功能层→封孔处理。过渡层选用粒径约70 μm的镍包铝粉末;功能层选用纯度为99.9%的氧化铝粉末,粒径约为30 μm;封孔剂选用KD-29。制备方法采用大气等离子喷涂技术,最终制备的氧化铝涂层孔隙率为2.82%,氧化铝层厚度约为500 μm,绝缘涂层整体厚度约为600 μm。制备绝缘涂层后,在陶瓷涂层表面制备镍膜,镀膜设备选用矩形靶磁控溅射镀膜机,靶材选用纯度为4 N、厚度为1.5 mm的平面镍靶。镀膜流程如下:1)对夹具以及固定架喷砂处理,除去表面残留的其他膜层,然后将样件置于无水乙醇、丙酮或去离子水中进行超声波清洗;3)镀膜机内不放置样件,将辅助阳极遮蔽,抽至不大于0.9×10-2Pa的真空;4)为去除靶材表面的氧化物等杂质,对靶材进行离子清洗,打开离子源挡板,设置离子源电流和电压,通入镀膜室的氩气流量为7.8 m3/h,清洗6 min;5)通入镀膜室的氩气流量为7.8 m3/h,加负偏压且逐渐提高负偏压值,清洗20 min,为防止电源损坏将电源电压控制在600 V以下,电压过大时应减小靶电流或提高氩气流量;6)靶材清洗后,打开镀膜机放入转架,打开辅助阳极,再次自动抽真空至0.9×10-2Pa,该阶段需控制镀膜室温度在150 ℃以下;7)为去除样件表面的氧化物等杂质以提升镍膜结合力,对样件进行离子清洗,设置氩气流量为7.8 m3/h,负偏压通过多个过渡阶段逐渐提升至450 V,清洗90 min;8)制备镍膜,镀膜后等镀膜室温冷却至100 ℃以下时取出样件。通过正交试验,分析工艺参数对镍膜表面形貌的影响和镀膜对绝缘涂层表面粗糙度的影响,以期得到最佳的工艺参数。根据相关研究及现有试验条件,选取靶电流、负偏压、溅射时间3个因素,每个因素取3个水平,因素水平见表1。为降低工艺优化的复杂程度,不考虑因素间的交互作用、三因素三水平问题,故选用L9(33)正交表,正交试验方案见表2。表1 正交试验优化设计因素及水平 Tab.1 Factors and levels of orthogonal test optimization design 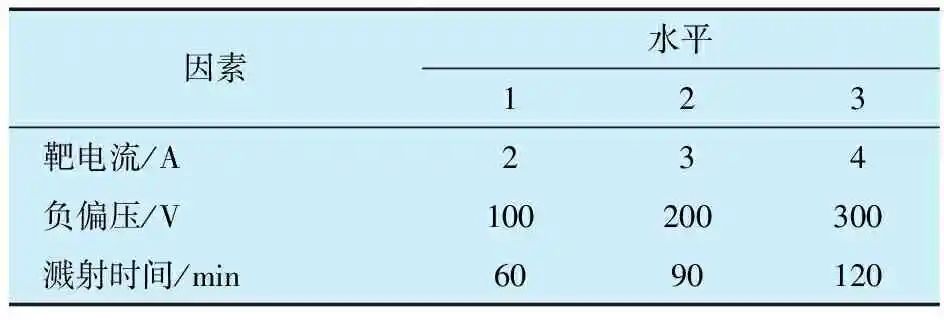
表2 正交试验方案 Tab.2 Orthogonal test plans 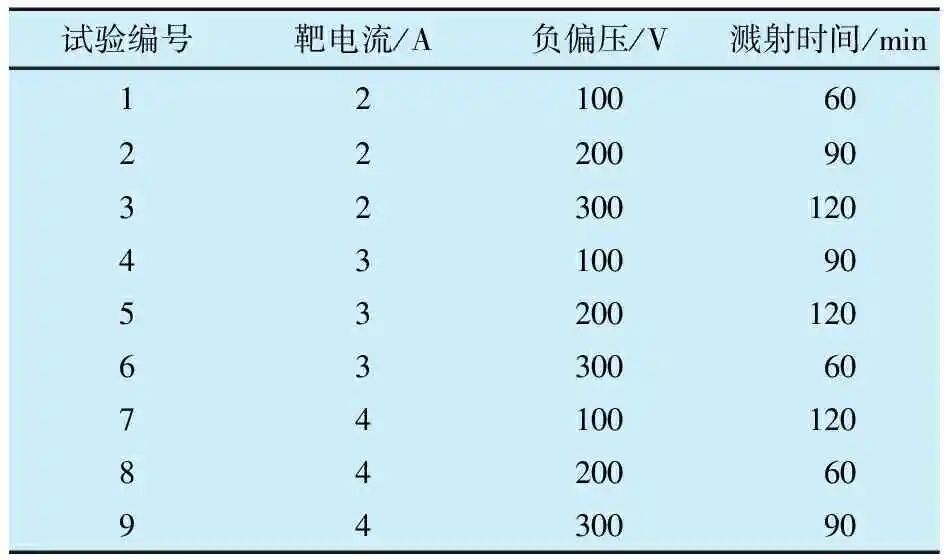
2 结果分析2.1 工艺参数对镍膜表面形貌的影响采用扫描电子显微镜分析镍膜的表面形貌,放大倍数为3 000,如图1所示:试验1,2,5,7制备的镍膜表面有大的裂纹与孔洞,质量较差;试验3,4制备的镍膜表面平整、光滑,局部存在较多小的孔隙和凹坑;试验6,8制备的镍膜表面连续性较好,膜层较为致密,仅在局部存在细小的裂纹;试验9制备的镍膜表面光滑,连续性好,膜层致密,质量最优。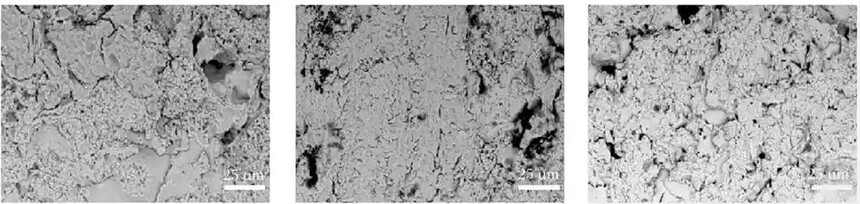
(a) 试验1 (b) 试验2 (c) 试验3 上述表面形貌特征说明:1)随靶电流增大,镍膜表面质量提高,这是因为随靶电流增大,氩原子的轰击能量增大,单位时间溅射的靶材原子增多,沉积到基体表面的粒子数增多,膜层更致密;2)随负偏压增大,镍膜表面质量提高,这是因为随负偏压增大,等离子体区域正离子对膜层的轰击能量增大,基体表面已沉积的松散的原子会被轰击掉,膜层表面在刻蚀作用下更加平整光滑[19];3)溅射时间对镍膜表面形貌影响较小,但溅射时间会影响镍膜厚度,不同工艺参数下的镍膜厚度见表3,随溅射时间增加,沉积到基体表面的靶材原子越多,镍膜厚度增大。
2.2 镀膜对绝缘涂层表面粗糙度的影响采用3D测量激光显微镜测试镍膜的三维形貌及表面粗糙度,三维形貌如图2所示,镀膜前后的表面粗糙度见表4。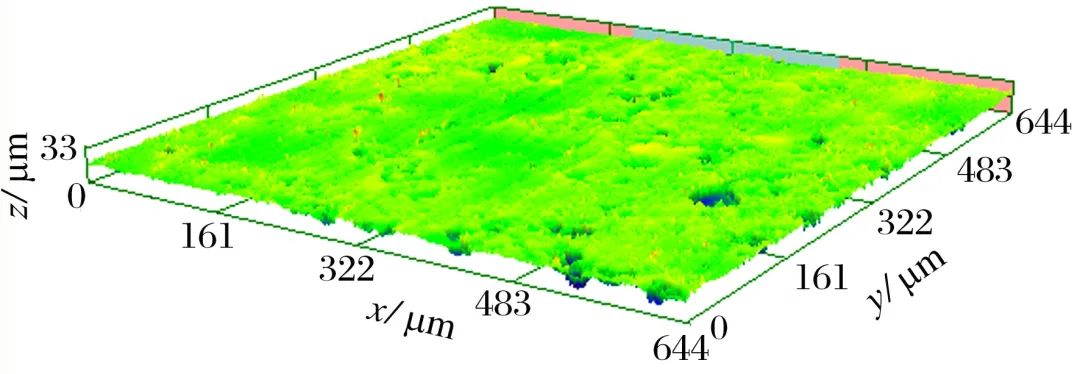
(a) 试验1 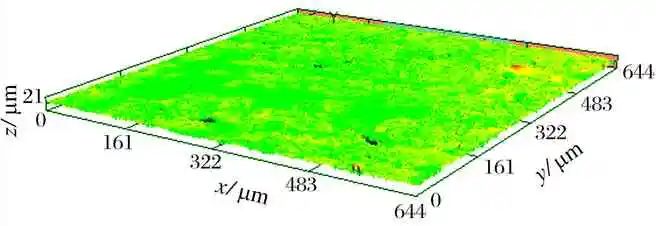
(b) 试验2 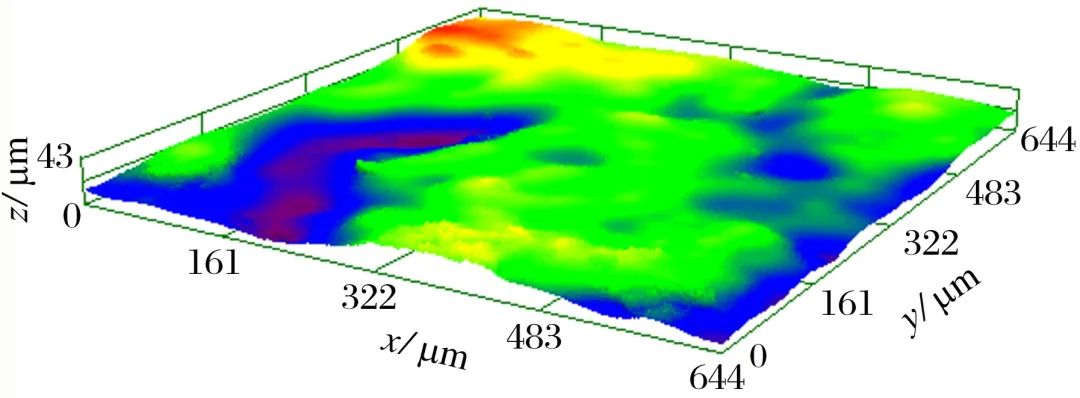
(c) 试验3 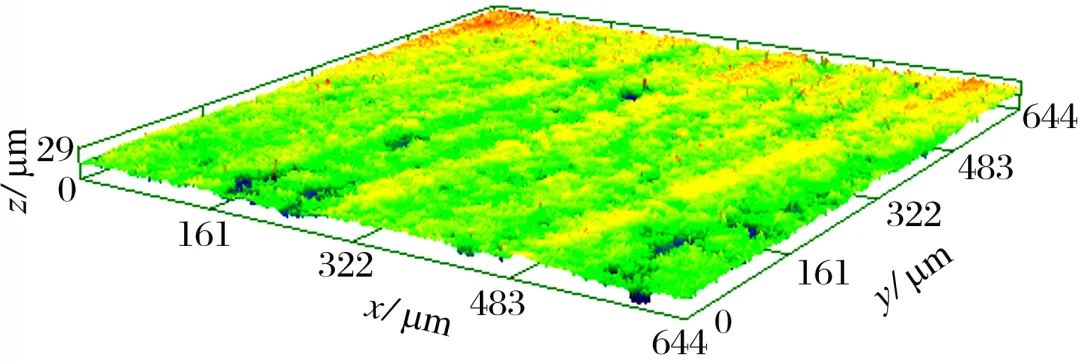
(d) 试验4 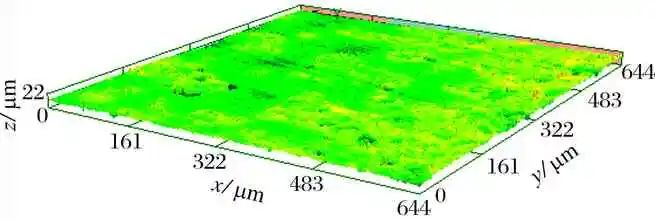
(e) 试验5 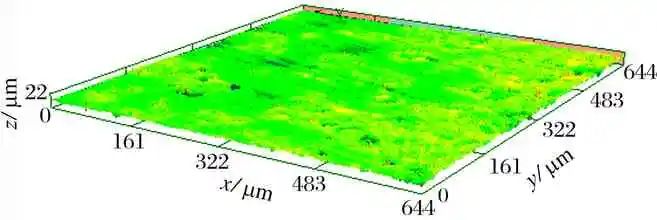
(f) 试验6 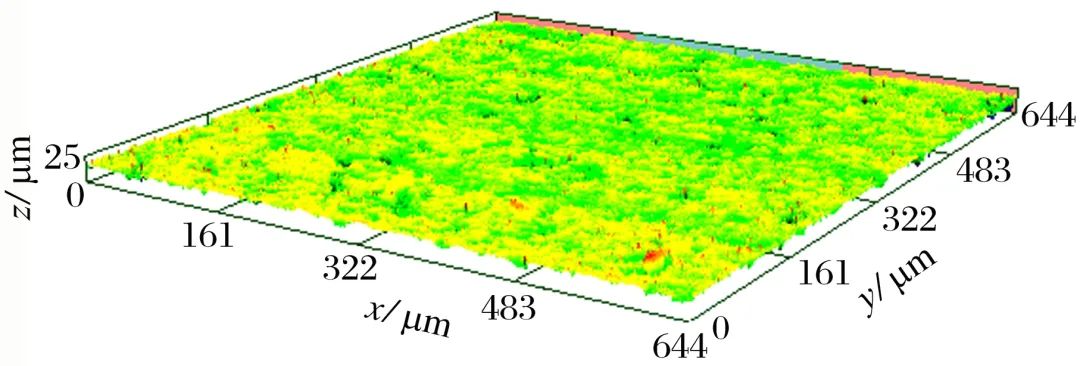
(g) 试验7 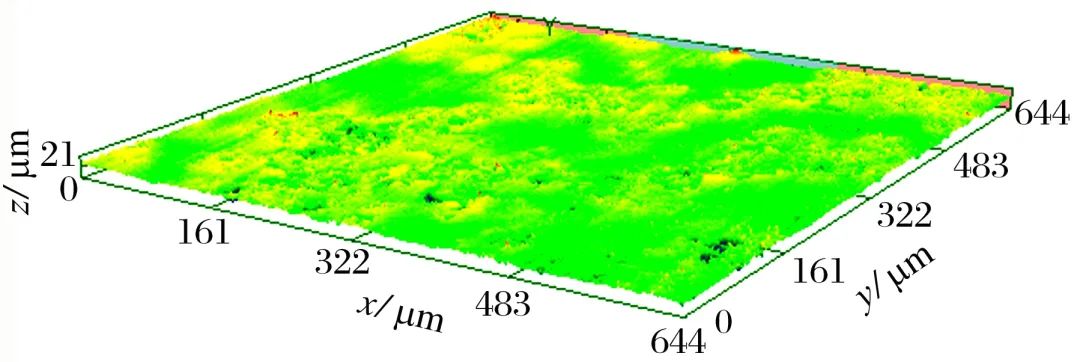
(h) 试验8 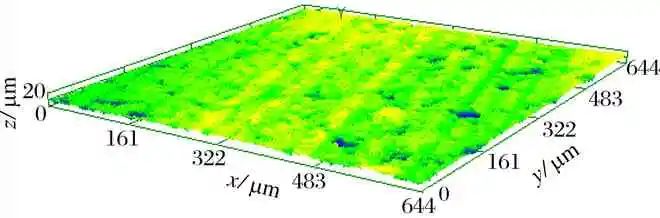
(i) 试验9 图2 不同工艺参数下镍膜的三维形貌 Fig.2 3D morphology of nickel film under different process parameters 表4 镀膜前后的表面粗糙度对比 Tab.4 Comparison of surface roughness before and after coating 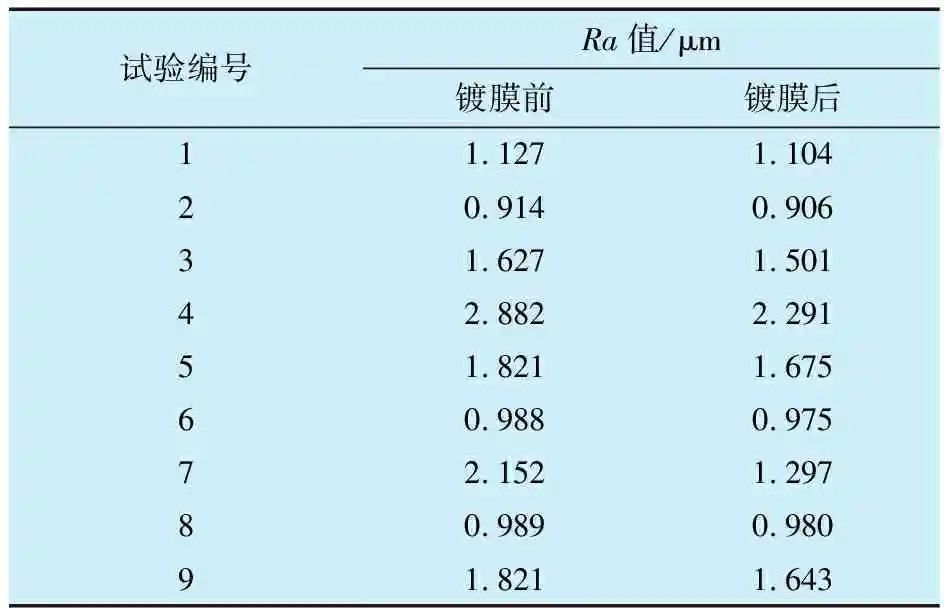 由图2及表4可知: 1)试验4镀膜前的表面粗糙度Ra值最大,镀膜后的表面粗糙度Ra值降至2.291 μm;2)试验2镀膜前的表面粗糙度Ra值最小,镀膜后的表面粗糙度Ra值降至0.906 μm;3)不同工艺参数下镀膜后的表面粗糙度值均小于镀膜前,说明在绝缘轴承陶瓷涂层表面制备镍膜可以改善其表面质量。2.3 小结综上分析可知:表面镍膜对绝缘涂层的表面粗糙度无负面影响,且可明显改善其表面质量,试验9镍膜表面光滑平整,连续性以及膜层致密性最优,故试验9工艺参数即为风电轴承套圈外表面镍膜制备的最佳工艺参数。3 镀膜对轴承绝缘性能的影响为分析镀膜对轴承绝缘性能的影响,参考GB/T 10580—2015《固体绝缘材料在试验前和试验时采用的标准条件》和GB/T 31838.4—2019《固体绝缘材料 介电和电阻特性 第4部分:电阻特性(DC方法) 绝缘电阻》,利用绝缘测试平台测试轴承绝缘性能。采用最佳工艺参数,在风电轴承外表面制备镍膜,具体工艺参数见表5。为防止镍膜镀在套圈内表面使内外表面导通进而降低绝缘性能,需制作盖板,使轴承套圈端面及内表面被遮蔽且保证外表面倒角处镍膜的完整性,夹具如图3所示,镀镍膜后的套圈如图4所示。表5 风电轴承外表面制备镍膜的工艺参数 Tab.5 Process parameters for preparation of nickel film on outer surface of wind turbine bearing 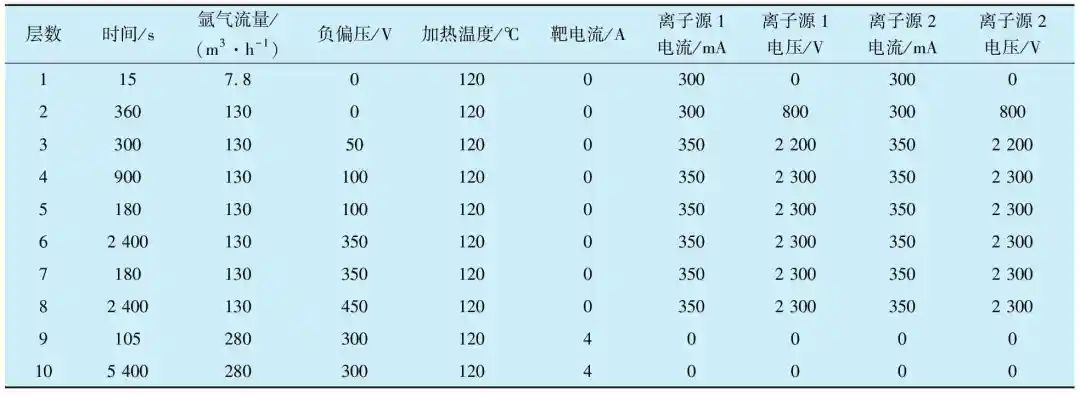
|
|